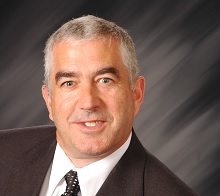
How is your hotel’s laundry running? I love asking this question. There’s no grey area on the answer. It’s either “not so great,” which means something is leaking and the technician has been here a scary long time. Or, “pretty good,” which means nothing is leaking. My response for the latter is “how do you know?”
As anybody in the lodging industry knows, being green isn’t a plug-and-play endeavor. It is a constant evolution. Why then is the laundry different? Why is it we buy a high G-force washer-extractor and a moisture-sensing tumble dryer and call our laundry “greened up?”
One Canadian property wasn’t willing to adopt that approach. Management wanted to ensure the laundry operated to its full potential, and opted to network washer-extractors and tumble dryers through a cutting-edge, cloud-based management system. Their goal was to leverage technology to better understand costs, and processes. When your property sits in a national park, green isn’t a marketing term; it’s part of the fabric of the hotel.
The 211-key Banff Park Lodge in Banff, Alberta, Canada, has been offering guests more than just breathtaking vistas; it has forged a reputation for excellence that extends from accommodations to its environmental achievements. The lodge is an Audubon International four Green Leaf property, and also is rated four Green Keys through the Hotel Association of Canada.
More Visibility into the Operation
As the property began to replace dated equipment with more efficient models, a management system that integrated with the machine controls would give greater visibility into the operation. Given the high employee turnover often seen in the hospitality laundry, additional oversight would be beneficial…and it was.
It wasn’t long after the property started generating laundry operations reports from its newly installed washers and dryers that management uncovered interesting data points. The first had to do with a discrepancy between the productivity of first and second shifts.
The non-supervised second shift was far less productive than the first shift, which is supervised. Armed with the data, management was able identify a situation where staff needed additional training. This is a prime example of how the system can serve as a flashlight to shine on areas requiring support. When best practices are followed, efficiency—both labor and utilities—goes up and laundries are able to get more done. Green knows no bounds and efficiency can extend into labor.
Additional early data showed the tumble dryers were being used twice as much as the washer-extractors. While the dryer situation ended up being a decision on the part of the laundry supervisor, the report data gave management a window into the operation it didn’t previously have.
The property will be adding additional networked machines to round out its replacement project. And from there, the staff will work to set a baseline for the operation that will drive key performance indicators on the overall health of the laundry.
Hard Data to Drive Greater Efficiency
In this industry, virtually everything has a metric tied to it. Management gets a variety of daily updates to ensure the overall health of the property. For years, the laundry room was the exception—with the basic metric of “is anything leaking or in need of repair? No? Then everything must be running fine.” Networking and reporting technology built into some modern equipment like UniMac and others changes all that. Now management has the hard data to ask questions and drive greater efficiency.
Don’t make the mistake that this is “Big Brother” software designed for the purpose of pointing fingers at staff. It’s not. At its best, a system like TotalVue creates opportunities to build a professional and well-trained staff that delivers consistently high quality results.
For those with multiple properties, the technology enables you to benchmark facilities against each other in simple dashboards, making it easy to compare utility consumption, productivity, expenses, and overall cost/pound to process loads.
It’s quite a simple formula—you can’t improve what you can’t measure. The network technology available on some models of laundry equipment finally delivers all the information operations need to improve overall efficiency through training and best practices. Now when asked the question, “how’s your hotel’s laundry running?” managers are able to answer confidently and have the hard data that shows the laundry as an extension of their green focus.
Bill Brooks is North American Sales Manager for the UniMac brand of laundry equipment.